The Future of Power Generation: The Data-driven Power Plant
June 12, 2015
on
on
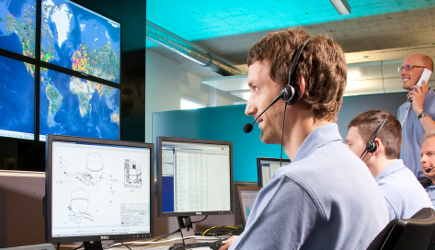
The energy transition is forcing utilities to rethink their power generating strategies. New applications of the industrial internet transform power plants into more flexible, reliable and cost-effective units.
The power generation landscape in Europe is going through a period of unprecedented change, on that most of the speakers at the annual PowerGen Europe conference held in Amsterdam this week agreed.
Only a decade ago electric utilities operated baseload power plants to meet the baseload requirement complemented with peaking units to meet spikes in demand. Baseload power plants, often coal-fired or nuclear, are build to run at near full annual capacity and can take days to ramp up and down. Peak units are mostly gas-fired and can quickly cycle up and down.
The rise of renewables with their low marginal costs is not only eating away at the market share of these central power plants, it also changes their role in the energy system. As more renewables come online fossil fueled power plants will increasingly serve as backup capacity, supplying to the grid on cloudy windless days.
Flexible generating capacity
As the decarbonization of the energy system progresses the need for flexible operating power plants increases while the use for baseload units decreases. Investments are needed to build up flexible generating capacity but there is little money to spare in the power generating industry that has seen wholesale power prices steadily declining since 2008.
At the same time, flexibility is one of the opportunities for fossil fueled power plants to make a profit. When the wind blows wholesale prices drop because every wind turbine is generating power, when the wind lies down prices go up, and it's the gas-fired power plant that can quickly ramp up that is going to make that sale.
What do you do when you haven't got the funds to update your hardware but need to get with the times? You bring in the software department.
The intelligent power plant
During the PowerGen conference General Electric's Power & Water devision presented a software platform that optimizes existing power plants.
“There is a lot of dark data”, said Dick Ayres, General Manager Software Solutions at GE Power Generation Services during the presentation. Maybe as much as 98% of the data produced by machines in the plant is not being used.
The purpose of GE's software platform is to bring that data together and mine it for outcomes. One machine may output data about an anomaly detection and another bleeps out a maintenance alert. Combining the data provides a holistic view of the state of the power plant and enables the operators to manage its performance better.
GE's platform was first installed in June 2014 at White Gate, a 445 MW gas-fired power plant in Ireland. When operating at full capacity the plant generates power for 300,000 households.
Data analytics help detect suboptimal performance of the plant. In White Gate a unit was detected that used 25% more gas than it ought to due to a wrongly set valve. The system also keeps track of parts degradation enabling timely maintenance to prevent costly unplanned shutdowns. In this sense GE's system saves costs.
But in the second phase of the implementation of the system, GE wants to help White Gate make money.
Further data-driven optimization could make the plant more efficient in terms of fuel burns during startup or reduce startup time to respond to the market faster.
And Dick Ayres wants even more data: “Integrating external datasets about the weather, market-level data and social data could provide new insights to be more efficient and capture new opportunities in the market place.”
Image: GE
The power generation landscape in Europe is going through a period of unprecedented change, on that most of the speakers at the annual PowerGen Europe conference held in Amsterdam this week agreed.
Only a decade ago electric utilities operated baseload power plants to meet the baseload requirement complemented with peaking units to meet spikes in demand. Baseload power plants, often coal-fired or nuclear, are build to run at near full annual capacity and can take days to ramp up and down. Peak units are mostly gas-fired and can quickly cycle up and down.
The rise of renewables with their low marginal costs is not only eating away at the market share of these central power plants, it also changes their role in the energy system. As more renewables come online fossil fueled power plants will increasingly serve as backup capacity, supplying to the grid on cloudy windless days.
Flexible generating capacity
As the decarbonization of the energy system progresses the need for flexible operating power plants increases while the use for baseload units decreases. Investments are needed to build up flexible generating capacity but there is little money to spare in the power generating industry that has seen wholesale power prices steadily declining since 2008.
At the same time, flexibility is one of the opportunities for fossil fueled power plants to make a profit. When the wind blows wholesale prices drop because every wind turbine is generating power, when the wind lies down prices go up, and it's the gas-fired power plant that can quickly ramp up that is going to make that sale.
What do you do when you haven't got the funds to update your hardware but need to get with the times? You bring in the software department.
The intelligent power plant
During the PowerGen conference General Electric's Power & Water devision presented a software platform that optimizes existing power plants.
“There is a lot of dark data”, said Dick Ayres, General Manager Software Solutions at GE Power Generation Services during the presentation. Maybe as much as 98% of the data produced by machines in the plant is not being used.
The purpose of GE's software platform is to bring that data together and mine it for outcomes. One machine may output data about an anomaly detection and another bleeps out a maintenance alert. Combining the data provides a holistic view of the state of the power plant and enables the operators to manage its performance better.
GE's platform was first installed in June 2014 at White Gate, a 445 MW gas-fired power plant in Ireland. When operating at full capacity the plant generates power for 300,000 households.
Data analytics help detect suboptimal performance of the plant. In White Gate a unit was detected that used 25% more gas than it ought to due to a wrongly set valve. The system also keeps track of parts degradation enabling timely maintenance to prevent costly unplanned shutdowns. In this sense GE's system saves costs.
But in the second phase of the implementation of the system, GE wants to help White Gate make money.
Further data-driven optimization could make the plant more efficient in terms of fuel burns during startup or reduce startup time to respond to the market faster.
And Dick Ayres wants even more data: “Integrating external datasets about the weather, market-level data and social data could provide new insights to be more efficient and capture new opportunities in the market place.”
Image: GE
Read full article
Hide full article
Discussion (1 comment)
Mohsen Pirmohammadi 9 years ago