A Test Engineer's Workspace for Innovative Electronics
on
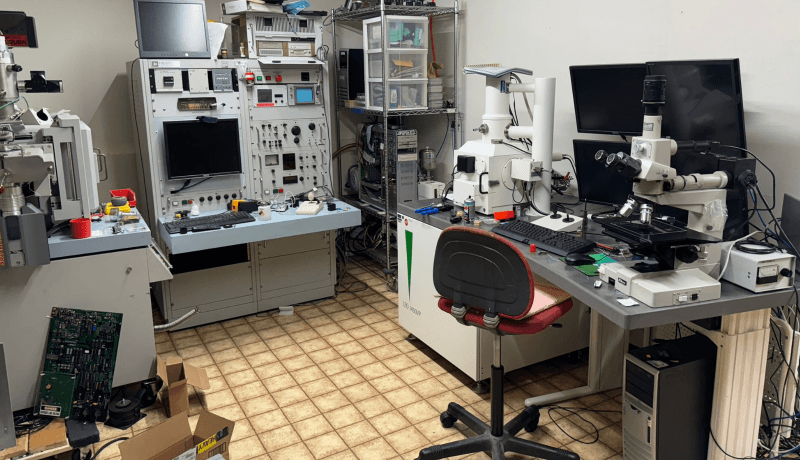
Discover a workspace that’s more than just a garage. Jerry Biehler, a Senior Test Engineer, has an electronics haven. From CNC mills and laser cutters to a scanning electron microscope (SEM) and focused ion beam (FIB) setup, every tool has a purpose. Jerry’s basement went viral on X, blowing up on my feed and sparking the start of our collaboration for this interview. What started as a casual scroll turned into a journey to discover this incredible setup!
What is your current occupation?
Jerry Biehler: Senior Test Engineer. I design test fixtures for laser micromachining systems and deal with component obsolescence. At home, I have a full machine shop with a CNC mill, toolroom lathe, tool grinder, laser cutter, and TIG welder. At another location, I have another lathe, another TIG machine, a MIG machine, a plasma cutter, etc.
In the lab area, I have my Leo 1450VP SEM, FEI FIB 611, and Nikon Optiphot 66. Another area has spectrometers, profilometers, radiation detection equipment, etc. The electronics area has a bench with scopes, meters, RF and function generators, and other tools. There’s also a large thermal evaporator with a Maglev turbo pump. I have a separate craft room where I work on cosplays for friends, and I also do cosplay photography.
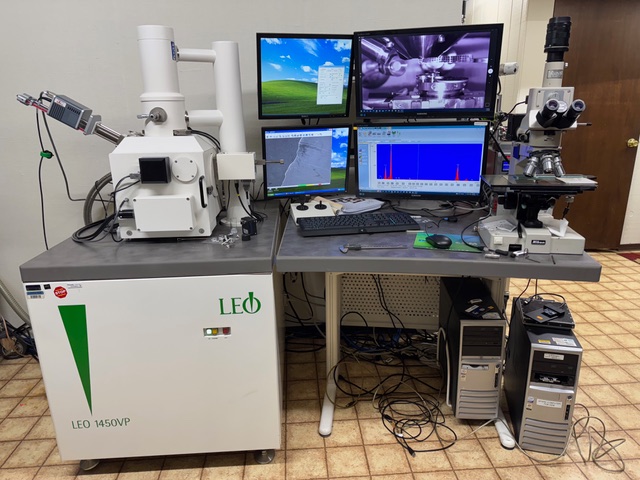
How would you best describe your workspace? How do you use it?
Jerry: Garage with machine tools, laser cutter, electronics bench, thermal evaporator, and 3D printers. Outside shed for storage, where the air compressor and vacuum pumps for the thermal evaporator live, as well as the filter for the laser cutter exhaust. The rest of the downstairs is lab space with the SEM, FIB, and other "clean" tools. Upstairs, I have a photo studio area and a craft room.
Where is your electronics-related space, and how long have you had it?
Jerry: My workspace takes up most of my house. I've had it for about 20 years, but after buying a new house two years ago, I moved everything over and expanded significantly, and I use it a few times per week.
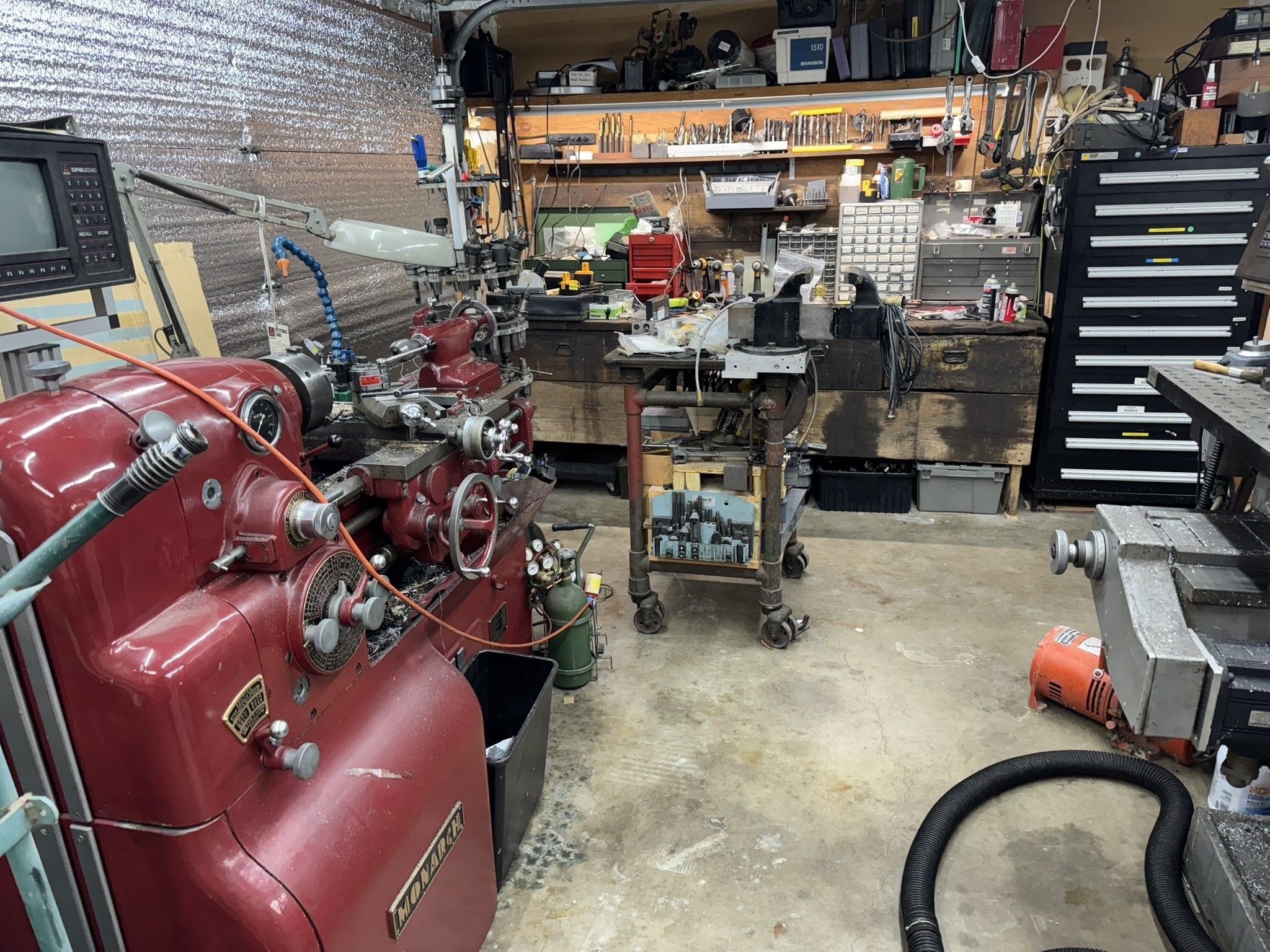
When you designed your workspace, what were your requirements and goals?
Jerry: Designed? Hah. It’s in a state of constant flux depending on what new equipment I get. There are four machines in the garage that are too heavy to move, plus things like my Vidmar drawers and great-grandpa’s workbench.
This summer, a lot of the downstairs was rearranged, removing a large vacuum system that was being set up for e-beam coating. It was traded for the FIB. Then I found a much newer SEM, so the electronics bench and cabinet got moved to the garage. I bought the house with the studio space upstairs in mind, as well as a dedicated craft room.
Do you enjoy learning about where other engineers and makers work on electronics projects? Take a look at these electronics workspaces.
Tell us about your technical interests. What sort of projects do you work on in your space? Why?
Jerry: Mostly digital electronics and mechanical engineering. My programming is awful, and I can get around and build things, but it isn’t pretty. I work with lasers, mechanical, electrical, vacuum, optics, computers, you name it.
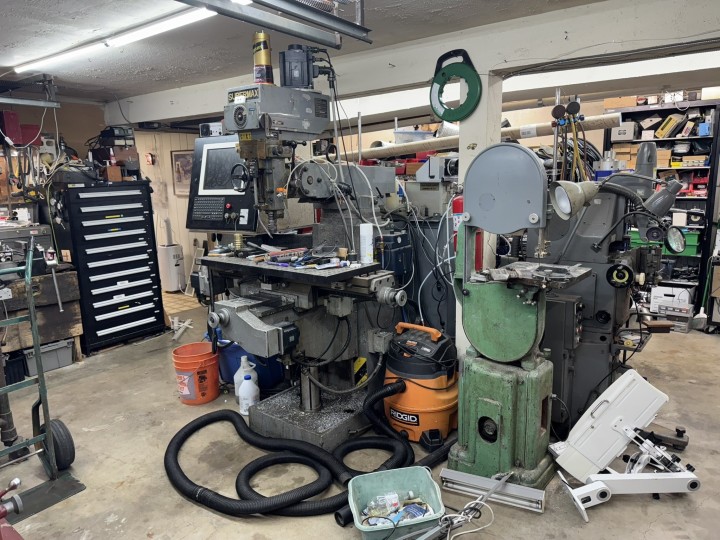
What sort of equipment and tools do you have in your workspace? How and where do you store them?
Jerry: On the bench: LeCroy Waverunner 64xi, Tek 2465, ESI 296 LCR, Metcal station with desolder and tweezers, Zeiss OPMI stereoscope, Keithley Sourcemeter, HP Function Generator, Gigatronics RF function gen, HP 34401A DMM, and a couple of rack-mount power supplies.
Machine shop: Monarch 10EE lathe, Supermax YCM-16VS mill (converted to CNC by Tektronix), Tsugami tool grinder, Thermal Arc 300 GTSW TIG welder, and a laser cutter built around a Coherent 150W CO2 laser that can cut thin steel and stainless.
Lab area: FEI FIB 611 Focused Ion Beam mill, a field emission SEM column waiting to go on, Zeiss Leo 1450VP Variable Pressure SEM with EDX, Ocean Optics USB-4000 spectrometer, large dual-grating UV-VIS scanning monochromator, and a Sloan Profilometer for measuring film thickness. The thermal evaporator is an 18" CHA-based system with an Adexian 2100 L/s maglev turbo pump, backed by a Leybold 30 rough pump and a Ruvac 101 roots blower. The coater has a planetary system and spots for boats. A Commonwealth ion beam gun is installed inside.
Craft room: Singer HD sewing machine and various benches.
Photo area: Photogenic strobes and Canon 5DII, 5DIII, and R6 cameras.
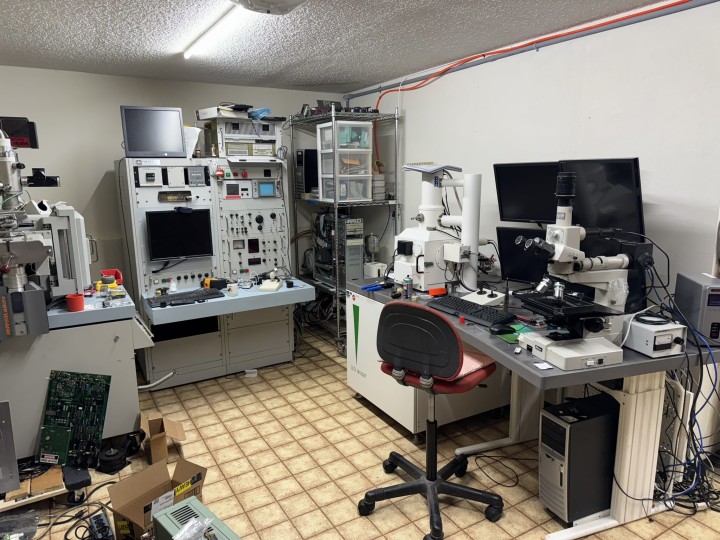
What do you consider your most important or valued piece of equipment or tool?
Jerry: They’re all important. I use the LeCroy scope more than the Tek. The CNC mill and lathe are very useful, as well as the laser. Being able to cut thin metal quickly and accurately makes all the difference. The SEM and FIB are mostly toys at this point, though some people want to use them for geological research.
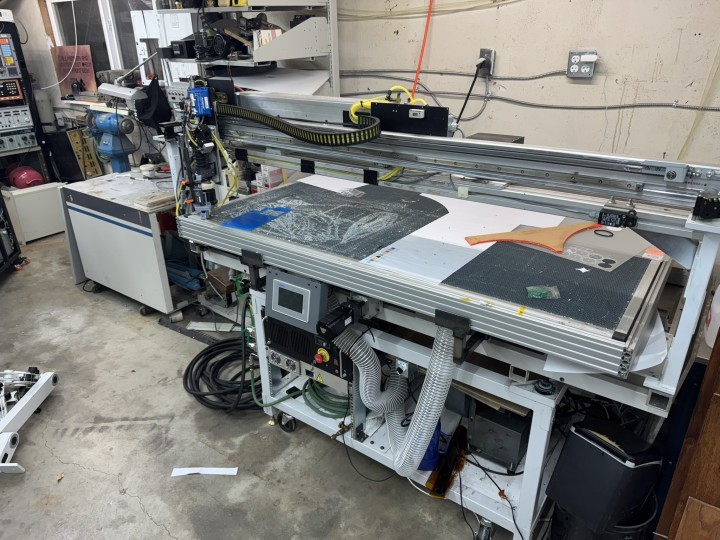
Is there anything special or unique about your workspace? What makes it special?
Jerry: I’ve modified the house to work with my tools and added a subpanel to the garage to feed all the tools. Installed the air compressor and vacuum pumps in the attached shed to reduce noise and save space. Added power for the SEM and FIB, routed compressed air throughout the downstairs, and installed nitrogen lines for the SEM and FIB. Tons of lighting in the garage, plus an ultrasonic humidifier fed from my RO water system to keep the humidity at a level where I’m not a walking Van de Graaff generator.
Are you planning anything new for your space?
Jerry: Everything is in a pretty good state right now. I need to move out the old SEM and move the console for the field emission column for the FIB to the lab area next to the FIB.
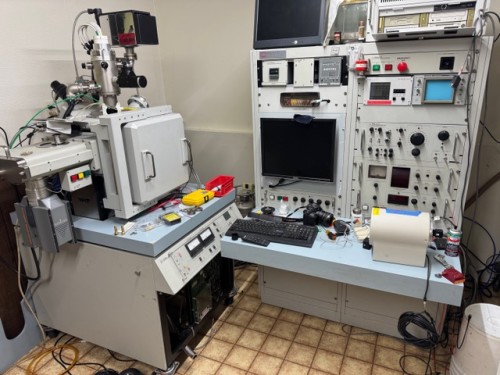
Tell us about your favorite electronics-related project. What components did you use?
Jerry: Most recent project was building a follow focus system for the laser cutter. It uses a Mitsubishi spoon connected to a Keyence displacement sensor to maintain the focus of the laser relative to the work surface. The data from the sensor is fed to a Teensy via serial, which then controls the servo drive for a small brushless motor with a ball screw that moves the cutting head up and down. A Clippard graphite piston air cylinder with a relieving pressure regulator balances the head to minimize the load on the servo motor.
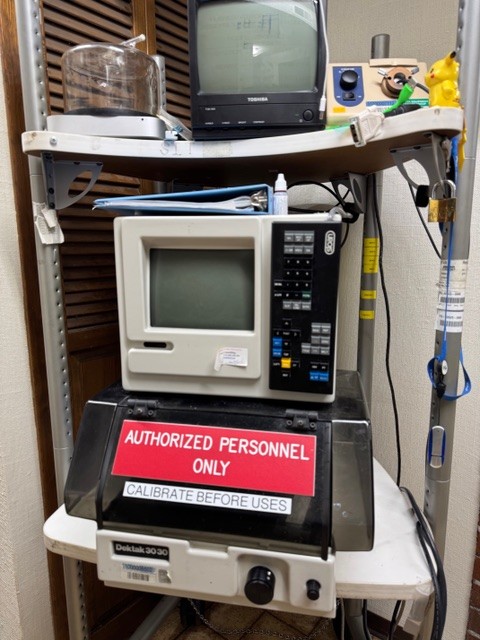
Are you currently working on an electronics or programming project?
Jerry: Currently repairing the EDX head on my SEM. The preamp ramp output was stuck at -14 V. Found it was overloading the 15 V from the external detector power supply. Checked with a thermal camera and found two hotspots, one was the 5 V LDO regulator, and the other was an area with no components.
Long story short: there’s -200 V used to bias the SDD sensor, and the trace was run inside the PCB, a layer away from the 5 V trace. A breakdown in the PCB caused the 5 V to short to ground: basically an FR4-based triode. I isolated the -200 V trace in that area and bypassed it with a wire, which seems to have solved the short issue. I replaced almost every IC on the PCBA and am waiting for one more IC before I can put it back together and test it.
Do you have a dream project or something you'd love to tackle?
Jerry: At this point, I have almost everything I can think of that I need. A lot of things are whims, whatever catches my eye at the time.
Do you have any advice, tips, or encouragement for other engineers or makers who are thinking of putting together a workspace?
Jerry: Get a good-paying job, lol. Don’t be afraid to break things. You WILL break things. Most things are fixable.
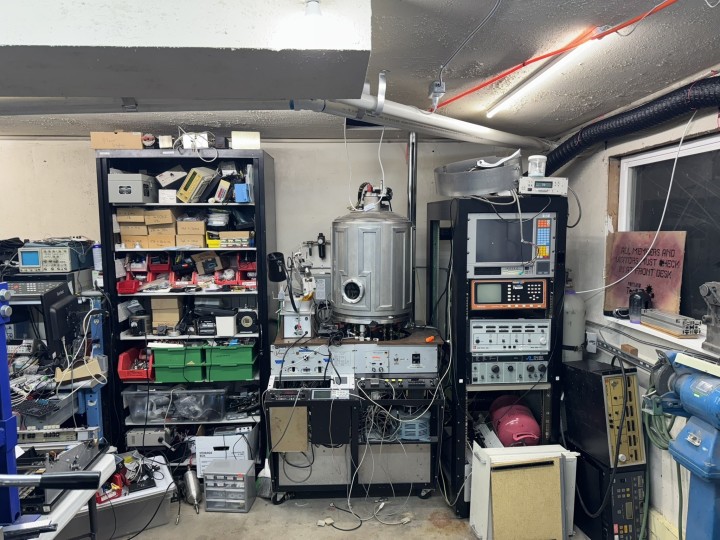
Show off Your Electronics Workspace!
Would you like to share details about your workspace with our global community of engineers, students, and makers? Take a few minutes to fill out this form so Elektor's editors can contact you!
Discussion (0 comments)