5V-1A Switch Mode Power Supply Design
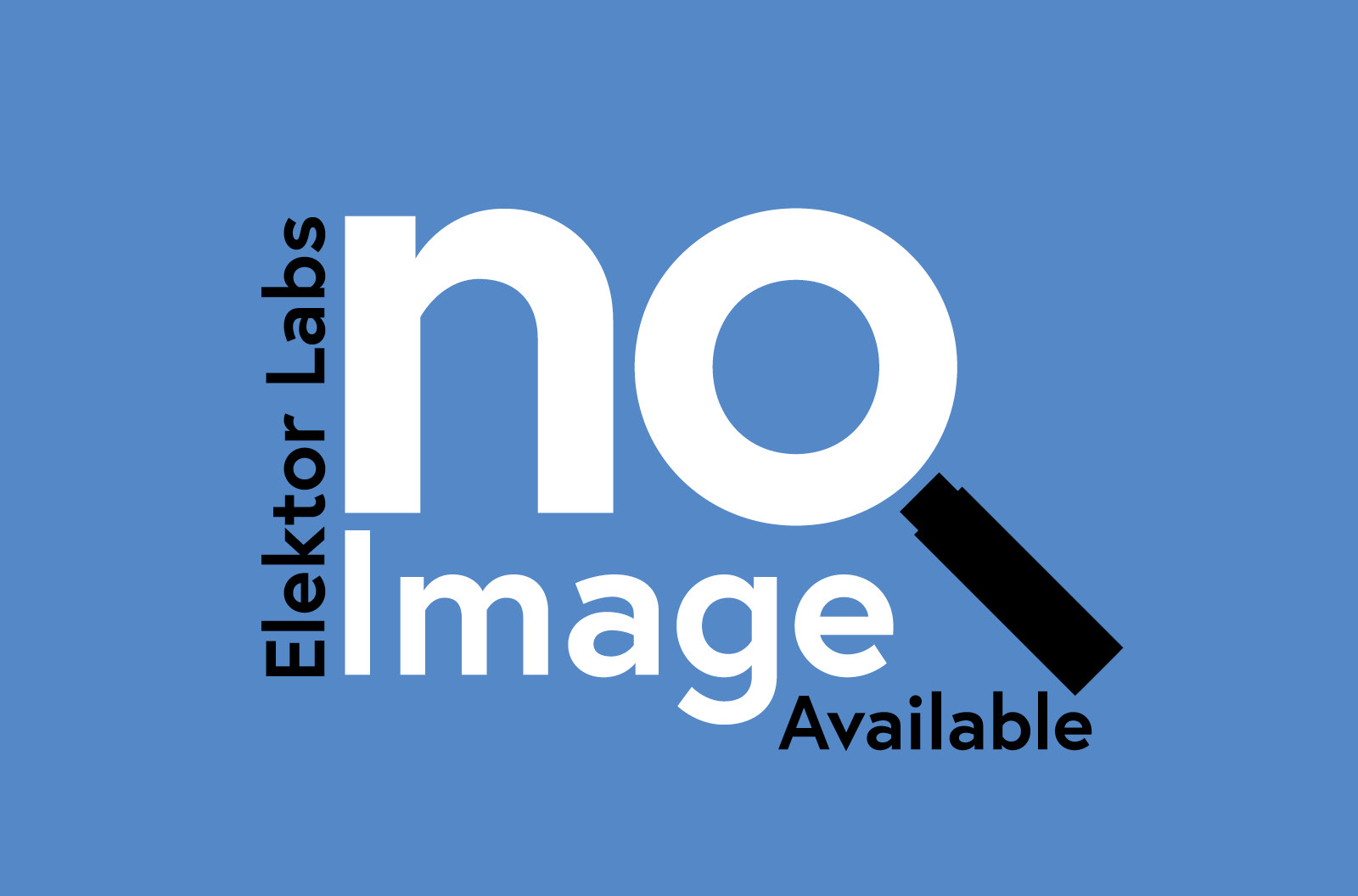
Switch mode power supply design example that describe the design process in 5 steps.
Switch mode power supply design example that describe the design process in 5 steps.
- Specifications
- Theorical design (Power stage)
- Theorical design (Controller stage)
- Simulation design
- Practical design
This converter generates an output voltage of 5V/1A, from an input voltage between 14V and 16V. This power supplies can use the 150100-I Versatile Switch Mode Power Supply PWM Controller.
PART 1 : Specifications
The power supply specifications are listed below.
- Input voltage : 15V +/-1V
- Output voltage : 5V +/-5%
- Output current : 1A max.
- Output ripple voltage : 100mV pkpk
- Output voltage drop : 200mV ( for an output current transient from 0.2A to 1A )
PART 2 : Theorical design (Power stage)
The power stage design is started with the choice of the operating mode, mode of control, switching frequency and the duty-cycle estimate. These parameters are used to estimate and to select all the power componnents.
Operating Mode
SMPS (Switch Mode Power Supplies) can operate from 2 different ways : either in CCM (Continuous Condution Mode) or in DCM (Condution Discontinuous Mode).
These 2 operating modes differ by the circulating current in the inductor (see [ADU], [ADU], ...).
In DCM the inductor current value return to zero at the end of each switching cycle.
In CCM the inductor current value stay at a non-zero value at the end of each switching cycle, this operating mode can simplify all calculus.
For the sake of simplicity, in this example, the CCM operating mode is used.
Switching frequency
The switching frequency is selected by compromise between a lot of parameter (size, efficiency, losses, EMC, etc.).
For this example, the switching frequency is selected arbitrary around 100kHz (switching period = 10 us).
Discussion (0 comments)