Recorder-like Electronic Musical Instrument (EWI) and MIDI Controller
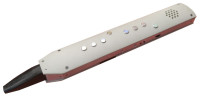
The "REMI" is an electronic wind instrument (EWI) with recorder-like fingering scheme. The design has evolved over the last few years and is now in its 3rd major revision.
REMI 3 - 'All-in-One' EWI
"REMI 3" is fully self-contained, battery-powered with built-in sound synthesizer, audio amplifier and speaker. It also has a 3.5mm headphone socket for private practice and a 1/4 inch phone jack for audio output to an instrument amplifier. A micro USB connector allows the REMI 3 to be used as a MIDI controller with a virtual synthesizer app on your computer or mobile device.
At the time of writing (Feb-2022), REMI model 3 is in the final stages of development. The prototype design is presented here for DIY electronics hobbyists who are capable of making their own. A printed circuit board and custom enclosure may be produced later to make construction easier.
Preliminary design notes are posted already on the author's website (link below). A complete article with detailed construction notes may be published if there is enough positive feedback from followers.
REMI 3 is based on the "Teensy 3.2" micro-controller module (from PJRC and Sparkfun). Software is developed in the Arduino IDE with "Teensyduino" code library.
The parts to build a REMI should cost much less than a commercial EWI.
REMI source code is freely available (for non-commercial purposes) allowing makers to tailor the firmware to suit their own design variants. (Latest firmware revisions are available on GitHub.)
"REMI 3" is fully self-contained, battery-powered with built-in sound synthesizer, audio amplifier and speaker. It also has a 3.5mm headphone socket for private practice and a 1/4 inch phone jack for audio output to an instrument amplifier. A micro USB connector allows the REMI 3 to be used as a MIDI controller with a virtual synthesizer app on your computer or mobile device.
At the time of writing (Feb-2022), REMI model 3 is in the final stages of development. The prototype design is presented here for DIY electronics hobbyists who are capable of making their own. A printed circuit board and custom enclosure may be produced later to make construction easier.
Preliminary design notes are posted already on the author's website (link below). A complete article with detailed construction notes may be published if there is enough positive feedback from followers.
REMI 3 is based on the "Teensy 3.2" micro-controller module (from PJRC and Sparkfun). Software is developed in the Arduino IDE with "Teensyduino" code library.
The parts to build a REMI should cost much less than a commercial EWI.
REMI source code is freely available (for non-commercial purposes) allowing makers to tailor the firmware to suit their own design variants. (Latest firmware revisions are available on GitHub.)
REMI 2 - EWI MIDI Controller
For makers preferring a simpler wind instrument that is easier to build, the "REMI mk2 handset" design is also presented here. REMI 2 is a MIDI wind controller with classic MIDI OUT connection ( 5-pin DIN socket). This model has no built-in synthesizer, but you can use it to play any MIDI synth or sound module, or connect to a computer via a low-cost USB-MIDI adapter.
Of course you could also build the companion ""REMI synth module" based on a PIC32MX MCU.
(See links further on.)
_______________________________________________________________
Original post (edited) -- relates to earlier REMI versions
The concept for the "REMI" came from a desire to create a simple but practical musical instrument which is easy to learn to play. An early design decision was to model the REMI loosely after existing “electronic wind instruments” (EWI's) using touch-sensitive pads for the “keys” to select the pitch of notes. A breath pressure sensor allows notes to be articulated by blowing into a mouth-piece.
Another major design decision was that the REMI need not emulate precisely the fingering scheme of a traditional wind instrument such as the saxophone, clarinet, flute or recorder (although a few minor design changes would make this possible). These instruments have complicated fingering schemes, of necessity, due to the physical properties of air columns made to produce sound. In contrast, electronic sound-generating devices are not constrained by such physical properties. Hence, a simplified fingering scheme based on the recorder was devised for the REMI. (See fingering charts.)
The instrument may consist of two main parts: a "handset" incorporating the touch-pads and other playing sensors and controls, plus a "controller module" housing a micro-processor, MIDI and audio circuitry and user interface components (LCD screen and keypad).
A push-button switch operated in conjunction with the touch-pads, selects one of several instrument "presets". The presets are chosen from a larger number of available instrument patches built into the micro-controller firmware. The "presets" also select one of a group of MIDI "programs" (instruments) for use with an external MIDI sound module.
Another design objective was that the synth module should be capable of generating a variety of instrument sounds, so that the REMI can be used "stand-alone", i.e. without needing to be plugged into an external MIDI synthesizer or computer. Further, a socket should be provided for direct audio output to an amplifier or headphones.
The remaining original text has been deleted because it is now largely obsolete. Please refer to updates by the author (below).
___________________________________________________________________________
Links
Introduction to the REMI project
Build the REMI mk2 (EWI MIDI controller)
Build the REMI Synth (MIDI Sound Module)
REMI 3 Prototype Design Notes
Updates from the author