Levitating Nanopositioner Boasts Nanometer Precision
on
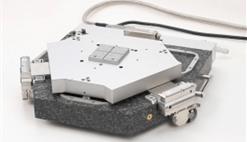
In cooperation with the Institute for Microelectronic and Mechatronic System and the Department of Mechatronics of Ilmenau University of Technology (Grmany), Physik Instrumente (PI) has designed a novel nanopositioning platform based on magnetic levitation. The platform utilizes a magnetic field that is generated by six coils and actively monitored by a 6D sensor. The magnetic field acts as a drive for the platform and actively guides the platform.
The magnetic field drive and the compact high-resolution measurement system with six degrees of freedom are designed to allow the platform to be passive, with no cable connections necessary. A two-dimensional optical incremental measurement system and capacitive sensors detect the platform position and control the drive in all axes. This allows objects to be moved linearly or rotationally on a plane with unprecedented positioning accuracy.
This nanopositioning system could replace the air-bearing systems and magnetic linear motors typically found in inspection and manufacturing systems used in the semiconductor industry. According to PI, if the platform moves on a circular path with a diameter of 100 nm, the maximum deviation from the ideal path is only a few nanometers. The current prototype has a motion range of 100 x 100 x0.15 mm and supports trajectories with nanometer precision at accelerations up to 2m/s² and velocities up to 100 mm/s. The digital motion controller, based on a modular system from PI, can process various types of geometry file as well as coordinate transformations.
Discussion (0 comments)