Electronic Equipment Repair: Tools, Techniques and Tips
on
Want to save money while extending the life of your electronic equipment? Repair your own tools and equipment! From mastering essential tools to explaining common component faults, this handy guide to electronic equipment repair will help to boost your confidence as you repair your devices.
First, let’s take a look at the tools that will be useful for most electronic repairs. Of course, everyone will have their list of favorite tools, according to personal preference. Here’s my list. If you’re a beginner, it may give you a few pointers to get you started. If you’ve only got one or two of these tools, and the list seems far too long or far too expensive, don’t panic! On the one hand, it’s always possible to do without, until you’ve decided that it’s the right time to buy a new tool, and, on the other hand, most of these things can be found either very cheaply in China, or at affordable prices on the second-hand market in any country.
Let’s start with the essential tools (Figure 1). You’ll need at least: a multimeter, a soldering iron and solder, an oscilloscope, and an adjustable power supply. To check solder joints and inspect the PCB for defects, a small magnifying glass with a high enough magnification (10× in my case) will be a precious help. Even a very inexpensive magnifier will be infinitely better than no magnifier at all; personally, I use a €3 plastic model from RS (ref 136-8106) which serves me well.
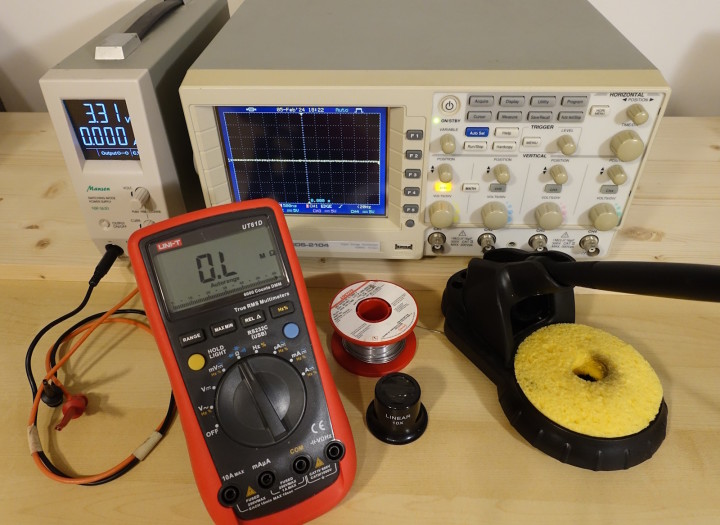
It’s debatable, but, in my opinion, a second multimeter and a second soldering iron are also essential tools. Two multimeters are useful at the same time, among other things for testing power supplies, by monitoring the output voltage while increasing output current. As for the second soldering iron, it will be almost irreplaceable as a complement to the first, for desoldering all kinds of SMD components with one iron in each hand.
Speaking of soldering, here are a few extra supplies. Desoldering braid (I recommend the tinned variant) and gel flux. For cleaning up after soldering, cotton swabs and 99% (or, failing that, 90%) isopropyl alcohol work well. I’d recommend putting the alcohol in small plastic bottles (50 or 100 ml, for example), allowing small quantities to be applied, and to devote one of these bottles to a 50% isopropyl/50% acetone mixture — very effective for hard-to-remove residue. Of course, if you can afford it, a professional cleaner such as Fluxclene is fine, but not essential. To remove severe corrosion caused by water ingress or electrolyte leakage from a capacitor, a fiberglass pencil brush comes in very handy.
Optional Tools to the Rescue
You can do without them, but once you’ve bought them, they turn out to be really useful. I recommend an inexpensive desoldering station. It’s so effective for cleanly and quickly desoldering transistors, capacitors, DIP ICs, connectors, relays, etc., that I think it would be a pity to go too long without one, especially with products as affordable as the ZD-915 or ZD-8915 models under €100. I would add to this category: an ESR or LCR meter, as well as a very cheap component tester such as the T4 model.
A Dim Bulb Current Limiter?
In the category of small, home-made tools that you build up over the course of your life, I’d also mention a dim bulb current limiter. It’s especially useful when repairing mains power supplies, particularly when these have faults such as short-circuited diode bridges or shorted transistors on the primary circuit, a blown fuse, etc. After repair, it’s a good idea to limit the maximum current, in case we’ve forgotten something, to prevent the same components from burning out again.
The principle is very simple: Put an incandescent bulb, with the appropriate voltage for mains power wherever you are on the planet, in series with one of the two power supply wires. In the event of a problem (at worst, a short circuit between live and neutral), there will be no more explosions; the lamp will simply light up, giving you time to disconnect without damage.
It’s a good idea to have several lamps of different wattages, so as to be able to limit the current to a higher or lower value, depending on the device you wish to test. This can be done very simply with a few spare bulbs and a bulb socket; you simply screw in the bulb of your choice as needed. Note that you need an incandescent bulb, not a CCFL or LED; to find one, you’ll maybe have to use the classified ads, as these have completely disappeared from store shelves in many countries.
For my part, I made a slightly more complicated setup than necessary (Figure 2), using a rotary switch to connect a number of small halogen bulbs in parallel (20 W / 230 V, G9), enabling me to limit the current in five steps — from 80 mA to around 400 mA.
Now, let’s talk about repair methods. Here are a few things you might find helpful.
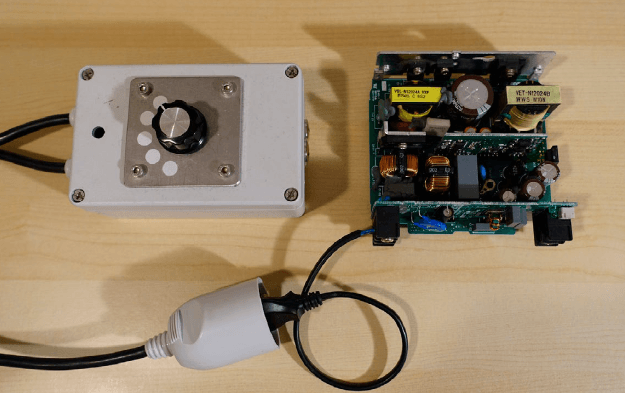
How to Tackle Electronic Repairs: A Few Hints
Start by taking stock of the situation. Do you know exactly what the fault is? If it’s a device you own, or one you were using yourself when the fault occurred, you probably have a pretty good idea. But take the time to make a note of it, noting anything that might be a clue. Does the unit have a display that indicates an error message? Does it run when cold and stop after warming up? Or vice versa? Has the unit suffered a shock? Does lightly tapping it affect its operation? All these clues will help you get started, so don’t overlook them. If possible, try to observe the fault yourself, if it’s a repair you’re doing for someone else.
Have a look on the internet to see if anyone else, in any forum, might have had the same problem on the same device. See if a service manual or schematics are available.
Next comes disassembly. Remember to take photos to make reassembly easier, and number the connectors on the cables with a fine-tipped permanent marker if necessary, so you can reattach them unambiguously on reassembly.
Two Past Repairs
Once, I troubleshot a Lithium battery-powered remote control for industrial equipment that refused to work. Everything on the board seemed to be inactive. No power, no reaction to button presses, even when replacing the battery with a power supply. In fact, a simple visual check revealed the solution: The central pin of the connector used to charge the battery was broken. As a result, the battery had discharged, and the battery charging/monitoring IC had put the whole board into deep sleep. To unlock this protection, you need to charge the battery, not with a lab power supply, but with the IC in question, which couldn’t happen with the pin missing. Keep your eyes open!
Another time, there was a rather complex motor controller which displayed “emergency stop switch engaged,” although this was not the case. I identified the terminal block dedicated to the emergency stop by consulting the manual, and followed the tracks back to one of the board’s microcontrollers, a good twenty centimeters away, checking numerous components along the way. I finally found a short-circuited transistor, just before the signal reached the microcontroller. Victory! This €1,500-plus device was finally repaired by replacing this 20-cent component.
Visual Inspection Comes First
For diagnosis, start with a good visual check: I’ve lost count of the number of times this has been able to tell me immediately, if not the precise fault, then at least its location on the PCB, thanks to burnt-out components, signs of overheating, missing components (component leads sometimes snap on impact, after having been fatigued by thermal cycling), cracked solder joints, and so on. Use your other senses too: a suspicious smell? A strange noise when you shake the case?
Try to identify functional blocks. Power supplies, front panel PCBs, digital control section, analog section, output stages if any, etc. Use deduction to locate possible sources of trouble.
Choose a direction: Either in the direction of flow (energy flow or information flow), or against the flow. From inputs to outputs, or vice versa. There are no hard and fast rules; at the beginning, you can choose arbitrarily, and alternate between the two techniques as the diagnosis progresses. For a power supply that doesn’t light up at all, it’s often convenient to start from the mains input, and check one after the other in the chain: fuse OK, diode bridge OK, PFC transistor OK, etc. On the other hand, if the power supply powers on but there’s a fault on just one of its multiple outputs, then it’s more relevant to start looking at the output, working backwards.
Is the Power On?
As a general rule, start by checking the power supply rails. Sometimes, there may be test points; otherwise, you can measure the voltage across the electrolytic capacitors. Common voltages are 12 V, 5 V, 3.3 V, etc. A fluctuating or absent voltage will alert you to a possible fault.
If the power supplies seem to be working, check that the functional blocks you come across are also powered, by measuring the voltages at the power supply terminals of the integrated circuits and microcontrollers. Datasheets and experience will tell you which pin numbers to look out for. In the event of zero voltage, use an ohmmeter to check that the rail is not short-circuited to ground. If it is, look for the short circuit; if it isn’t, look upstream to find out why the power supply isn’t turned on.
Whenever possible, I try to desolder as few components as possible. Nevertheless, it often happens that there’s a doubt, and you have to desolder a component to confirm a measurement, especially when looking for short-circuits. Beware! I’ve often come across PCBs without silk-screening, and it can happen to anyone to accidentally solder a SO-8 or SO-14 integrated circuit rotated, leading to anger and frustration on the next test. Refer to the photos taken beforehand.
In this phase of troubleshooting, it’s likely that you’ll have to alternate frequently between in-circuit component testing (without power), desoldering, re-soldering, possibly swapping components, testing with power on, and so on. In all cases, take your time and keep a clear head. Above all, never solder or desolder on a live circuit! And make sure it doesn’t happen either by accident. Apart from the safety issue, there’s a very real risk of creating faults by short-circuiting two adjacent pads with the iron.
Measuring Safely
Never take oscilloscope measurements on the primary side (mains side, before the transformer) of a power supply, unless you are fully informed and fairly experienced with differential probes and isolation transformers. On the secondary side, there are fewer safety risks, but still a risk of creating faults. Rather than taking the chance of slipping with the probe tip, I often prefer to solder a small piece of wire to the node of interest, and hook the probe to it. Another option is to use good quality, thin mini-grabbers, like the ones from EZ-Hook (see Figure 3). This leaves my hands free to operate the on/off button and the oscilloscope controls.
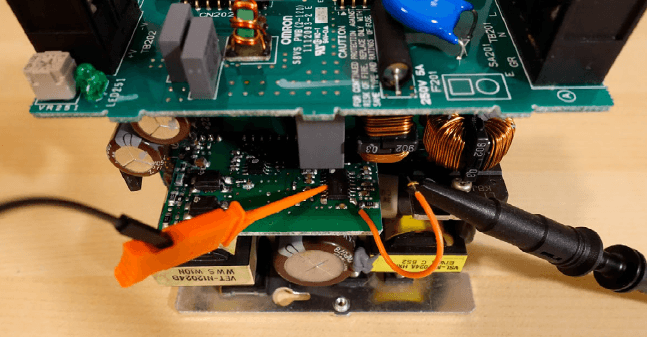
When I worked in an electronics repair shop, I used my computer all the time to look for the datasheets and pinouts of the countless new components I didn’t know about when repairing a particular device. When working without schematics, which are rarely available, and sometimes on PCBs without a silkscreen, SMD marking catalogs are invaluable tools to identify components. "SMD Marketing Codes" and "SMD Codebook" are two well-known examples, and there are others too.
Finally, there comes the moment when you’ve found a faulty component. No doubt, your measurements are categorical: It’s burnt out. Congratulations! Search the surrounding area, on all the tracks leading from all the pads of that component for any other damage.
Replacing Components
To replace the component, try as far as possible to replace it with an identical one, by searching all the usual suppliers: Farnell, RS, Mouser, Digikey, Distrelec, etc. If possible, avoid eBay and Aliexpress, where the probability of receiving a counterfeit component is sometimes as high as 100%.
If the component is difficult to source or obsolete, there is no choice but to find an equivalent. Pay attention to the type of package, its pinout, as well as the main characteristics: maximum voltage and current for transistors, switching speed, and so on. If in doubt, don’t hesitate to ask for help in a forum, where members are generally very helpful and friendly.
In the following section, let’s have a look at a few common faults that can happen for some of the more common components, as well as a few tips about testing them.
Failure Modes of Common Components
It can be useful to have an idea of the types of failure that can occur in a given type of component so that you can search effectively. It’s common to hear that electrolytic capacitors are always the culprits. This is sometimes true of very inexpensive switch-mode power supplies, which are built with capacitors limited to 85°C instead of the slightly more expensive ones that can withstand 105°C. Often, there is very little margin, in terms of both voltage and capacitance; this excessively strains the capacitors, which will generally give up and fail just after the expiry of the legal warranty. However, in better-designed devices, or in test and measurement instruments and industrial equipment, this is far from being the general case. Here’s a list of common failures, classified by component type.
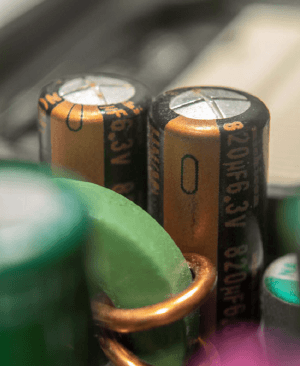
Electrolytic capacitors: Sometimes bulging, as shown in Figure 4, or having lost electrolyte, lost capacitance or having an ESR value too high. Test with a multimeter in capacitor mode, an ESR meter, or an LCR meter. Those that are bulging or have leaked need to be replaced without further testing; for those with a normal appearance, desolder one lead to prevent neighboring components from interfering with the measurement.
Power transistors (bipolar or MOSFET): Often short-circuited, sometimes open-circuited. Test with multimeter diode mode. Identify the pinout first. For a bipolar transistor, check the base-emitter and base-collector junctions. Also check that there is no continuity between collector and emitter. For a MOSFET, check that the MOSFET’s internal diode is visible (junction voltage around 0.5 or 0.6 V) between Drain and Source (Figure 5), and that the gate is isolated from the other two pins.
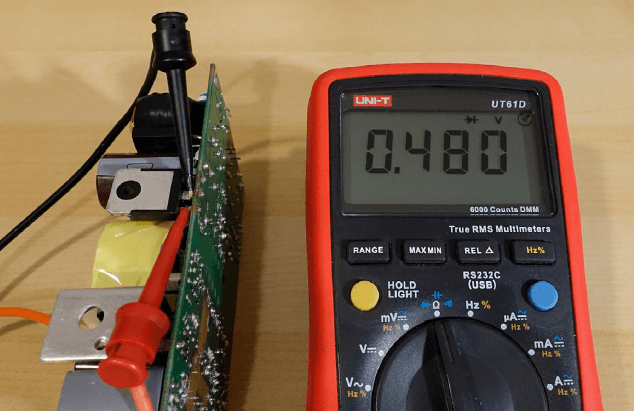
Power diodes, rectifier diode bridges: Often short-circuited, more rarely open-circuited. When tested in diode mode, you should find a voltage of around 0.6 or 0.7 V for conventional diodes in the forward direction, and OL (infinity) in the reverse direction. For Schottky diodes, the voltage is lower, down to around 0.3 V.
Power resistors: Often open. Typical case: resistors used to limit the start-up current of some switch-mode power supplies.
Through-hole or SMD diodes, or Zener diodes, and small bipolar or MOSFET transistors: Short-circuited or open-circuited. Test them using the Diode mode.
Power ICs: Meaning those which can potentially dissipate some heat, such as motor drivers: Supply pins short-circuited to ground, or output pins short-circuited to ground or VCC. This is often the case with switching-controller ICs, on the primary side of switching power supplies. In particular, those incorporating the control logic and power transistor in the same package (such as ST’s VIPER20 and others) are fragile.
Plastic film capacitors: Loss of capacitance. More rarely, short-circuited. Capacitance loss is frequent, especially when these capacitors are used as capacitive droppers, i.e., to obtain a voltage of a few volts to supply a logic circuit from the mains. In this case, a constant AC current flows permanently through the capacitor, which will age prematurely.
Transformers: Open-circuit, or short-circuit between turns (leading to overcurrent and overheating).
Through-hole or SMD resistors: Sometimes visibly burnt out, sometimes open-circuited, not visible to the naked eye. That can be checked easily with an ohmmeter: Due to the various components in parallel with the resistor under test, the resistance measured must always be lower than the value shown on the resistor marking. If this is not the case, the resistor is open-circuited or has drifted upwards considerably.
SMD ceramic capacitors: Sometimes short-circuited. In this case, the entire supply rail is shorted to ground. To locate it on the board, you can use a lab power supply. Set the voltage to a low value, such as 1 V or 2 V, and the maximum current to about 1 A. Connect it to the power rail, while respecting the polarity. This will force current into the short-circuit. Then, use the DMM in millivoltmeter mode to get closer and closer to the short-circuit. The voltage is lowest across the short-circuited capacitor. Some people recommend using a beefier power supply and setting the current to a higher value; this can make the short-circuited component warm up, and it can then be seen with a thermal camera. If you use this technique, be careful, a higher current could also burn some tracks instead. In very rare occasions, these caps can also go open circuit — see the text frame about the power supply for an example.
Relays: Their contacts can become resistive after a large number of actuations. This can be checked with the ohmmeter on the contacts, by supplying the relay coil with the appropriate voltage from a lab power supply. Take care to use the correct voltage for the coil, and the correct polarity, to avoid damaging the rest of the circuit. The (+) can usually be found by looking at which of the two coil terminals is connected to the cathode of the freewheeling diode, which is often located nearby. If in doubt, unsolder the relay to test it safely outside the circuit.
Push-buttons: Sometimes short-circuited (causing erratic device operation), or sometimes no longer making any contact (the device no longer responds), especially when they have been in contact with water.
Solder joints: Some lead-free alloys are prone to cracking with age, as a result of repeated thermal cycling. These can be hard to see with the naked eye, but a hair-thin crack can be enough to break continuity completely. This shows the importance of inspecting the entire board with a magnifying glass. An example of rather big cracks is visible in Figure 6. Other, much thinner, ones are much harder to find.
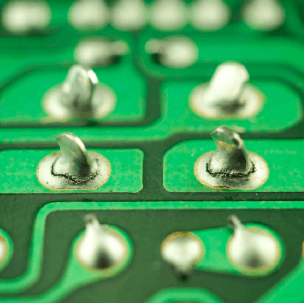
Quartz crystals: They are generally reliable, but may stop oscillating after a shock. If the microcontroller to which a quartz is connected is active, with some LEDs flashing or something showing on the LCD, you know the crystal is working. If no such activity is visible, the easiest way is to probe one of its terminals with an oscilloscope, relative to ground. Then move the probe to the second terminal. You should find a stable oscillation, at least a few hundred millivolts in amplitude, at the frequency marked on the quartz. One of the signals will have a larger amplitude than the other — this is normal.
Note: An 10× probe should be used for this to avoid disturbing the oscillation too much. Sometimes, the input capacitance of the oscilloscope probe stops the oscillation of a quartz crystal, even though the quartz is fine. In this case, try again on the second terminal: This time, you should see an oscillation. Oscillators often have an input side with a high impedance, on which this can occur. The output side, with its lower impedance, is less easily disturbed. If you don’t see anything on any of the terminals, either the microcontroller is not powered on or the quartz is defective.
Other faults: In an industrial electronics repair shop, we come across failures that are a little different from those encountered in consumer electronics. For example, liquid damage is very common, due to water penetration when machines are washed. As the equipment is often live, with high voltages (400 V AC) and circuit breakers rated for substantial currents, the damage can be severe. I often encountered burn marks, vaporized tracks/wires/connectors, open NTC thermistors, short-circuited MOVs, as well as severe oxidation on tracks, pads and components. Finally, connectors were often oxidized, or caused poor contacts, having become loose due to vibration. This frequently leads to arcing between adjacent pins.
Electronic Equipment Repair: Looking Ahead
Now you should be able to approach repairs with more confidence and serenity. I strongly encourage you to give it a go — the results and the satisfaction you’ll derive from them are well worth the effort. Also, don’t hesitate to check out the forums and YouTube, where you’ll find some very interesting content. Each of the electronics specialists on YouTube has their own personality and their own, often different, methods — that’s what makes it so rich. For example, when it comes to repairing test and measurement instruments, some videos from The Signal Path, or Feedback Loop, are inspiring; when it comes to switching power supplies, DiodeGoneWild produces videos packed with information; and finally, for retro computing enthusiasts, take a look at Tony359’s videos. Good luck with your repairs, and have fun!
A Power Supply That Wouldn't Cooperate
That one gave me a hard time. I troubleshot an ATX PC power supply, a CX400 from Corsair, dating from the 2010s. It was shutting down after some time. The first problem was that the power supply was willing to switch on in the PC, but categorically refused to start up on my workbench when I used the classic technique of shorting the green PS_ON wire to ground, which complicated my diagnosis. Being less experienced at the time, I didn’t immediately think of connecting an additional resistive load on the 5V_SB rail (standby supply) to remedy this.
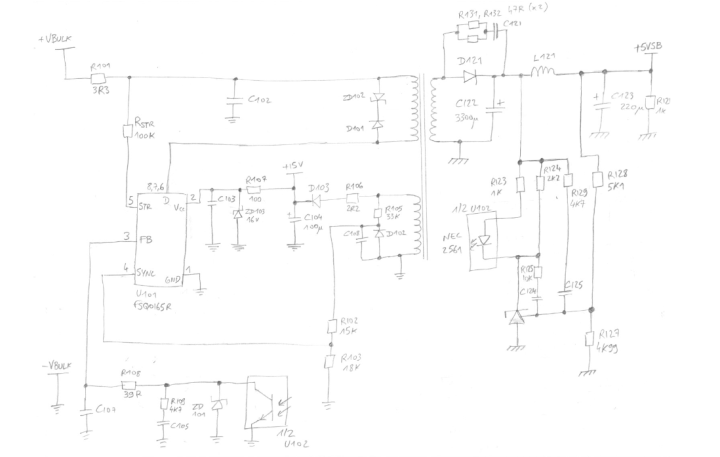
Having done this, I noticed considerable instability in the 5V_SB voltage, with sawtooth fluctuations of several volts in amplitude. Yet all the infamous electrolytic capacitors were in good condition on the output (and on the other outputs too). To help me troubleshoot, I made a hand-drawn snippet of schematic, as shown opposite. I highly recommend you do the same when you get stuck; schematics, even incomplete and hand-drawn, are always helpful.
In fact, there was a small SMD ceramic capacitor, C107 on the previous figure, which was part of an RC low-pass filter, in the voltage feedback loop of this rail. This capacitor had gone open, and was no longer filtering anything, causing the instability. A very rare failure! A few years later, while browsing a forum, I came across someone who’d had the same problem, with the same component in the same power supply. That was probably a manufacturing defect that caused the capacitor to crack due to thermal cycling.
A Few Additional Tips and Tricks
- Use the sharpest probe tips possible, to overcome the oxidation layer on solder joints and make reliable measurements on components without having to press too hard. This reduces the risk of slipping. Cheap multimeter probe tips are often made of plated brass and tend to dull quickly. For my part, I use Hirschmann PRUEF 2 stainless steel tips. They are very sharp, and I regularly re-sharpen them on a small whetstone.
- When component markings are made difficult to read by a thick clear varnish, called “conformal coating,” acetone can often be used to remove it and see more clearly. Use cotton swabs and a hard wooden tool such as a chopstick to scrape. Don’t use a metal tool, which will scratch the surface of the component and make it even more difficult to read the marking.
- Some switch-mode power supplies require a minimum load to operate. A suitable power resistor will do, but is not always included on the PCB itself. Think about this if the power supply you’re troubleshooting can’t start up or fails to regulate its output voltage properly.
- Sometimes, before being wave-soldered, SMD components are glued with a dot of red glue to hold them when they’re upside-down. They are tricky to desolder without damaging the component and the pads. Heat all the terminals at the same time with a large soldering tip and plenty of solder. For small 2-terminal components, a “knife” tip can work well to heat both sides simultaneously. For bigger components, use two soldering irons. While heating, gently insert an X-ACTO blade under the component to detach the glue.
- Beware of charged capacitors! In particular, bulk capacitors on the primary side of switch-mode power supplies are often charged to 325 V DC. There is sometimes a dedicated resistor to discharge them when the mains is switched off, but not always. Before any test or measurement, check with a multimeter that they are completely discharged, and discharge them if necessary. I use a pair of multimeter probes connected together via a 2.7 kΩ / 5 W resistor, as shown in the photo opposite. Don’t do this with a screwdriver, as it will damage the screwdriver, the solder joint and also the capacitor due to the sudden current spike.
- To open snap-on enclosures made of plastic, don’t use a screwdriver, as it leaves dents in the plastic. You can buy dedicated spudgers which are wider, and thin and flexible, to avoid marking. I use an old paring knife from my kitchen, which I purposely de-sharpened completely with sandpaper, to make it totally harmless.
- Leaded solder can be easier to use to prototype new circuits and general DIY work, and I try to use it whenever possible. It can be difficult to buy due to RoHS restrictions, though. Note that mixing leaded and lead-free when reworking a solder joint yields poor results and should be avoided. Either buy a roll of each, or carefully remove all the lead-free solder residue before re-soldering with the leaded alloy. In any case, choose a good brand, such as Loctite, Kester, Stannol, etc. from a well-known retailer; avoid unknown brands from AliExpress.
Editor's note: This article (240069-01) appears in Elektor May/June 2024.
Discussion (5 comments)