How the Voltera NOVA Speeds Up Innovation in Wearable Electronic Systems
on
Rapid Prototyping of Flexible, Stretchable Electronics
Most of your experience with printed circuit boards (PCB) will be with green FR4 substrates. This copper-clad industry classic is turned into the desired design by removing the excess copper. But, like in the world of 3D printing, there are those working on systems that print PCBs. This enables researchers to replace the rigid FR4 in favor of flexible, stretchable substrates.
Electronics has burrowed its way into almost every aspect of our lives. In fact, finding anything that doesn’t rely on electronics in some way is difficult. And while traditional circuit manufacturing materials and processes are optimized for their needs, medical electronics researchers often find them to be sub-optimal, especially when building systems designed to be worn. Human and animal bodies are non-uniform, with skin stretching when in motion that needs to be accommodated by an electronic application. Flexible PCBs have been around for a long time, using FR4 boards bonded to one another via copper tracks on polyimide, also known as Kapton. But while plenty of flex motion is available, the material doesn’t stretch.
Flexible electronics is possible; it’s just challenging to manufacture and out of the scope of most prototyping teams. For example, thermoplastic polyurethane (TPU) is both flexible and stretchable, and conductors can be applied using a metal deposition process known as sputtering. In a vacuum, the material’s surface is bombarded with gaseous ions accelerated by a high voltage. Upon arrival, they form a tight bond with the target material. This method is often used to apply aluminum or alloys such as tungsten-titanium, or aluminum-copper. Otherwise, it’s back to screen printing, something you probably last tried at school. Like printing posters or t-shirts, conductive inks are applied to the substrate through a mask applied to a pre-tensioned steel or nylon mesh before heating the ink to cure it.
Additive Approach to Circuit Manufacture
This makes the prototyping process either slow and expensive or slow and messy. However, this is changing thanks to the development of PCB printers, replicating the growth in 3D printers for plastic. Using Direct Ink Writing (DIW), these machines use an additive, rather than a subtractive, approach to apply conductive material where it is needed.
There are two types of rapid prototyping circuit printing approaches on the market. The first uses positive displacement, similar to a medical syringe. The ink is placed inside the barrel with a plastic or rubber plunger head pressed against it. Discounting the complexities of the fluid dynamics of conductive inks, this method is relatively reliable. A specific displacement on the plunger consistently delivers the same amount of ink through the nozzle. Clogging can be an issue, but this is a challenge for any dispenser working with thixotropic materials (fluids whose viscosity changes when sheared). Additionally, for self-filled barrels, trapped air can alter your flow rate. Storage between use can also throw up challenges. The ink may have to be refrigerated or frozen, although some inks can be stored at room temperature.
The other approach is thermal inkjet, where cartridges containing conductive ink print onto the target substrate. As a technology, it can achieve fine-printed features when adequately tuned and can be used with both rigid and flexible substrates. However, compatible inks have relatively low viscosities, making fewer options available. There are also other challenges. Low ink viscosities can lead to beading up or spreading out on some substrates, resulting in poor adhesion unless special coatings are applied. And, because much of the ink is solvent, cured printed features often leave little conductive material behind. Issues with solderability and higher-than-desired track resistance may result. Multi-pass printing can combat this, but may impact minimum feature size due to alignment errors. Nozzle clogging is another frustration. Inks destabilize if incorrectly stored, causing blockages due to the formation of agglomerates. And even if storage recommendations are followed, heat from the thermal inkjetting process will cure some ink in the nozzles.
NOVA — A Modular Dispensing Platform
Tackling the challenges of rapid prototyping of flexible circuits is Voltera, the Canadian scale-up that launched the V-One around seven years ago. That printer primarily targeted rigid substrates, although users were creating flexible circuits too. With NOVA , their newest printer launched late last year, they’ve gone all-in on supporting flexible, stretchable electronics (Figure 1).
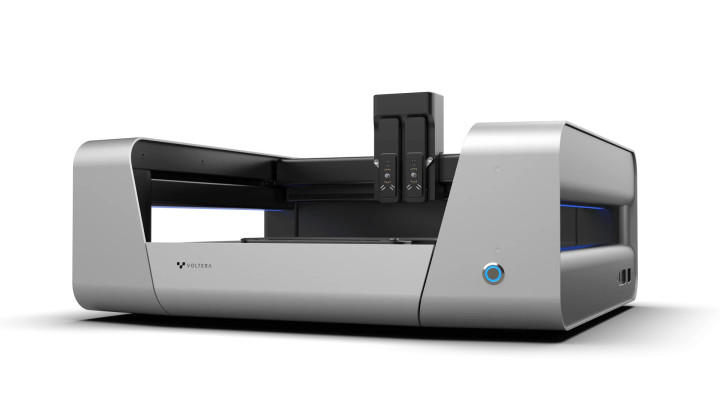
Leveraging their knowledge of positive displacement printing, they’ve retained the syringe-style dispensers. However, the hardware is significantly upgraded, with a pressure feedback loop integrated into the printing head. There is also a 12 W heater that holds the ink’s temperature at a constant value, ensuring a more consistent dispensing result during application. Incredibly, even air conditioning variations between rooms can result in differences in how the ink will dispense. Bearing in mind the wide variety of substrates and inks they are trying to support, users can quickly trial materials with viscosities ranging from 1,000 to 1,000,000 cP (centipoise). So, while silver-based inks such as the Conductor 3 are readily available and suitable for both rigid and flexible applications, you can also fill a barrel with the same conductive inks used for screen-printed electronics to meet your own needs.
NOVA weighs in at 35 kg, meaning you’ll need somewhere permanent to house it. And, at 675×605×345 mm, that’s going to be most of a table. At the front, a drawer provides space to store materials and tools. Inside, a foam inlay ensures the print head and surface probe are securely stored alongside the other tools you’ll need at hand during operation.
While the unit sports an Ethernet socket, the user guide recommends plugging in the Wi-Fi dongle included and using this to access the printer. Instead of providing software to install on your PC, this device is browser-based. That means, regardless of your chosen operating system and computer manufacturer, you won’t have problems operating the printer. Furthermore, in a lab environment, everyone can access the unit as needed. However, if Wi-Fi isn’t your thing, there is that provision for a wired Ethernet cable.
Keeping Flexible Substrates in Place
Your flexible substrate is held in place by the porous titanium print bed with an integrated vacuum pump, large enough to handle anything up to A4 size. This stops the material from curling during printing and provides a better fixture solution than clamping. The module port is affixed to an X-Y-Z gantry that simultaneously accommodates two tools. These consist of the Smart Dispenser and the Smart Probe (Figure 2). The latter features a ruby-tipped probe that precisely maps the substrate’s surface. Tools are easily affixed and detached thanks to the kinematic coupling and locking levers. Integrated LEDs provide the user with the tool’s status.
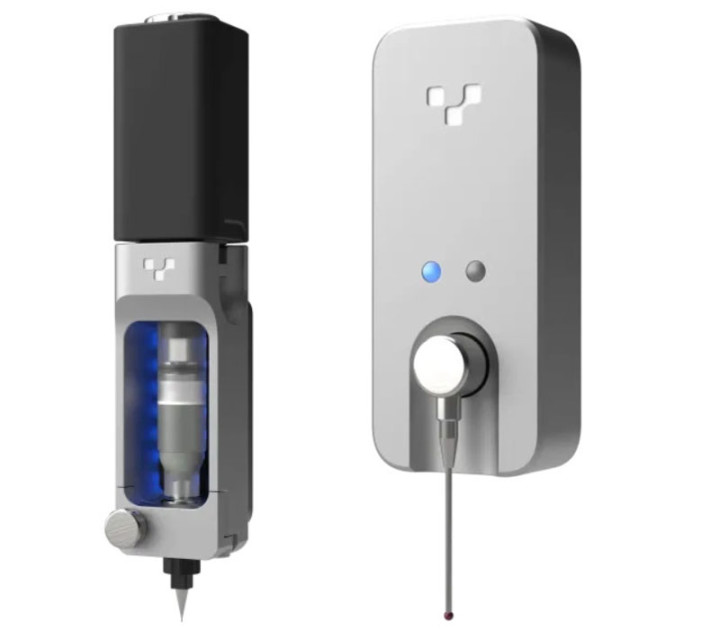
The Smart Dispenser has a pressure sensor used for closed-loop feedback during operation to provide a consistent ink flow. The syringe barrels are standard 5 cc types that can be filled with 2.5 ml of ink, with replacements available from Voltera and its partners. Tracks down to 0.1 mm can be printed, while pads for surface mount devices with a pitch of 0.4 mm are supported with the right combination of nozzle and ink. A selection of nozzles, 100 µm, 150 µm, and 225 µm, are available. However, thanks to the use of luer lock syringe barrels, any standard nozzle can be used, ensuring that the optimal combination can be found for the selected ink to achieve the track dimensions you require.
By far, the most significant benefit of the NOVA is its flexibility when testing inks with substrates. Depending on the composition, the ink may only be suitable for rigid substrates. Others may be usable on flexible but not stretchable materials. Polyimide (flexible) and TPU (stretchable) are popular materials, but you’ll also need to ensure that the ink wets to the surface. There are also those experimenting with paper, which is porous. If the ink soaks in, there is a risk that conductive pathways fail to form. In such cases, coated papers can be the answer.
Camera-Supported Calibration
Before printing starts, an AI-enabled calibration process is executed (Figure 3). Patterns are printed onto a dedicated, removable calibration plate, rather than the target substrate that is integrated in the unit. This avoids the need to clean the target substrate, an alternative calibration target, before printing. NOVA also integrates an 8-megapixel camera that takes photos of the calibration print. After each attempt, the image is shown in the user interface, making it much easier to determine if dispensing has been tuned to your needs.
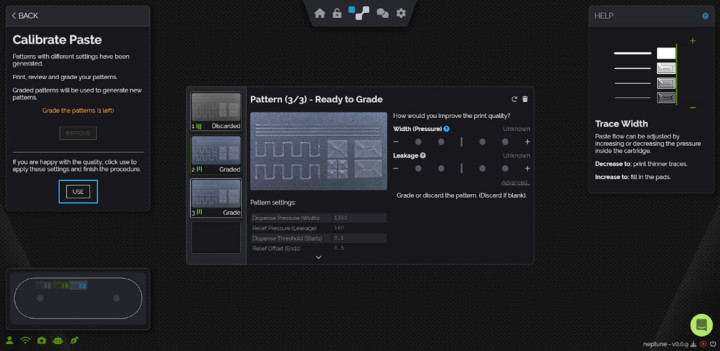
Curing and Soldering
After printing, the next step is curing, and, for this, a separate oven will be needed. As an example, Conductor 3 ink for flexible circuits has been designed to cure following a profile of 90°C for five minutes, followed by 120°C for 20 minutes, a little more than half the time needed for the previous ink generation. It’s important to understand that the curing process is there to evaporate the ink’s solvents, leaving the remaining binder polymers to hold the conductive filler particles in place. Because of this, the thickness of your tracks may be reduced during this process.
Some applications only require the conductive tracks to be applied to a flexible or stretchable substrate. But others may need some components added. Depending on the ink used, you may need to burnish the solder pads prior to soldering. Additionally, soldering temperatures often need to be lowered to protect both the electrical tracks and the substrate. As an example, Conductor 3 ink doesn’t require burnishing. However, a tin-bismuth-silver (SnBiAg) solder or solder paste will be needed, together with a soldering iron tip or reflow soldering profile temperature of just 180 °C.
Other methods for attaching flexible or stretchable materials to your electronic circuit include compression fixtures, conductive glues, or the creation of a tail for a zero insertion force connector, which may also need the inclusion of a stiffener.
First Attempts With Stretchable PCBs
The Voltera team has been working hard to research the optimal combinations of substrates and inks by trialing wearable applications. One of these was an insole pressure sensor for shoes to help measure weight distribution and monitor posture and gait problems (Figure 4). The prototype design uses Celanese Intexar TPU film and Intexar PE874 stretchable silver conductive ink from the same supplier. The printed sensor and a carbon film layer were connected to an Arduino Mega, enabling pressure results to be graphed.
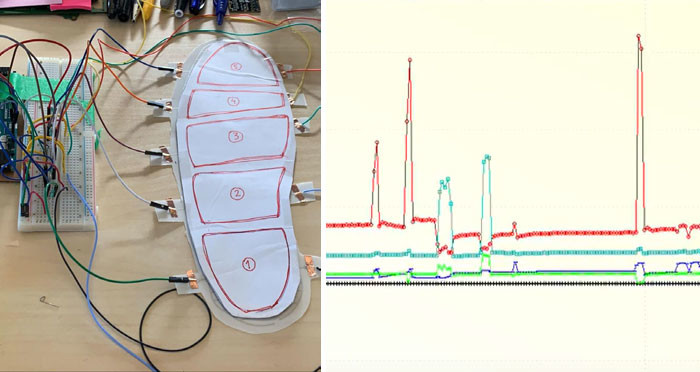
Another project used the same materials to create a heater for integration into clothing (Figure 5). The heater is laminated onto the cloth using a T-shirt press commonly used for transferring pictures, while a mechanical compression joint allows power to be applied. Stretchable substrates can also be printed with conductive ink to create strain gauges. This phenomenon was used to good effect in a control glove for a robotic hand (Figure 6). Thicker tracks proved to provide a more consistent output, while MG Chemicals 9400 conductive adhesive allowed wires to be connected to the sensors.
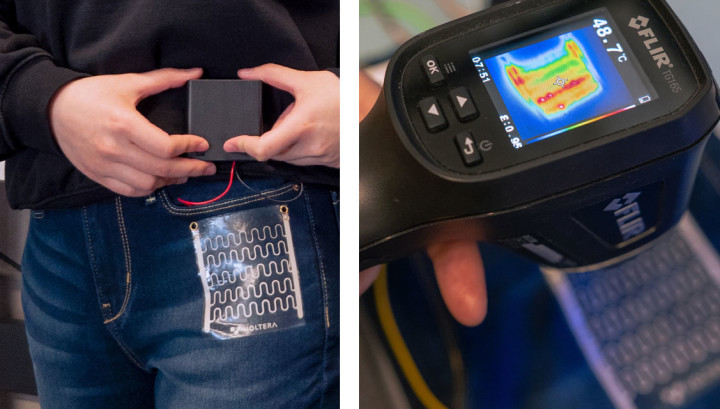
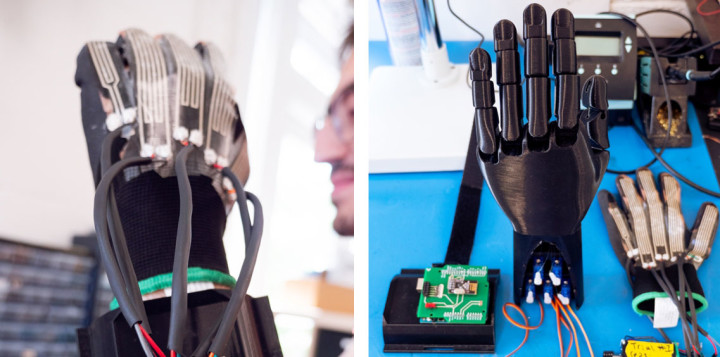
Additive PCB printer technology allows researchers and engineering teams to shorten development times and iterate their ideas much faster. Conductive inks can even be used to fix mistakes in a PCB design by simply printing missing or additional tracks, then curing. Wearable electronics have long been a challenge. This is because the truly stretchable electronics for use close to the skin were only manufacturable using expensive metal sputtering techniques or messy screen-printing processes. Now, with the Voltera NOVA, researchers can innovate and create prototypes in-house in numbers large enough for meaningful trials at a fraction of the cost.
Elektor Expert Paper
Elektor has seen unprecedented demand for printed circuit board (PCB) printers over the past few months. Not unsurprisingly, there has been a flood of questions on the technology too. With prices starting at four figures, purchasers naturally want to be sure they are investing in the optimal technology for their needs. To support our Elektor members and valued customers, we have drawn all the available knowledge together in a buyer’s guide, a living document that we will keep updated as the market evolves and matures.
Click here for more details
Discussion (0 comments)